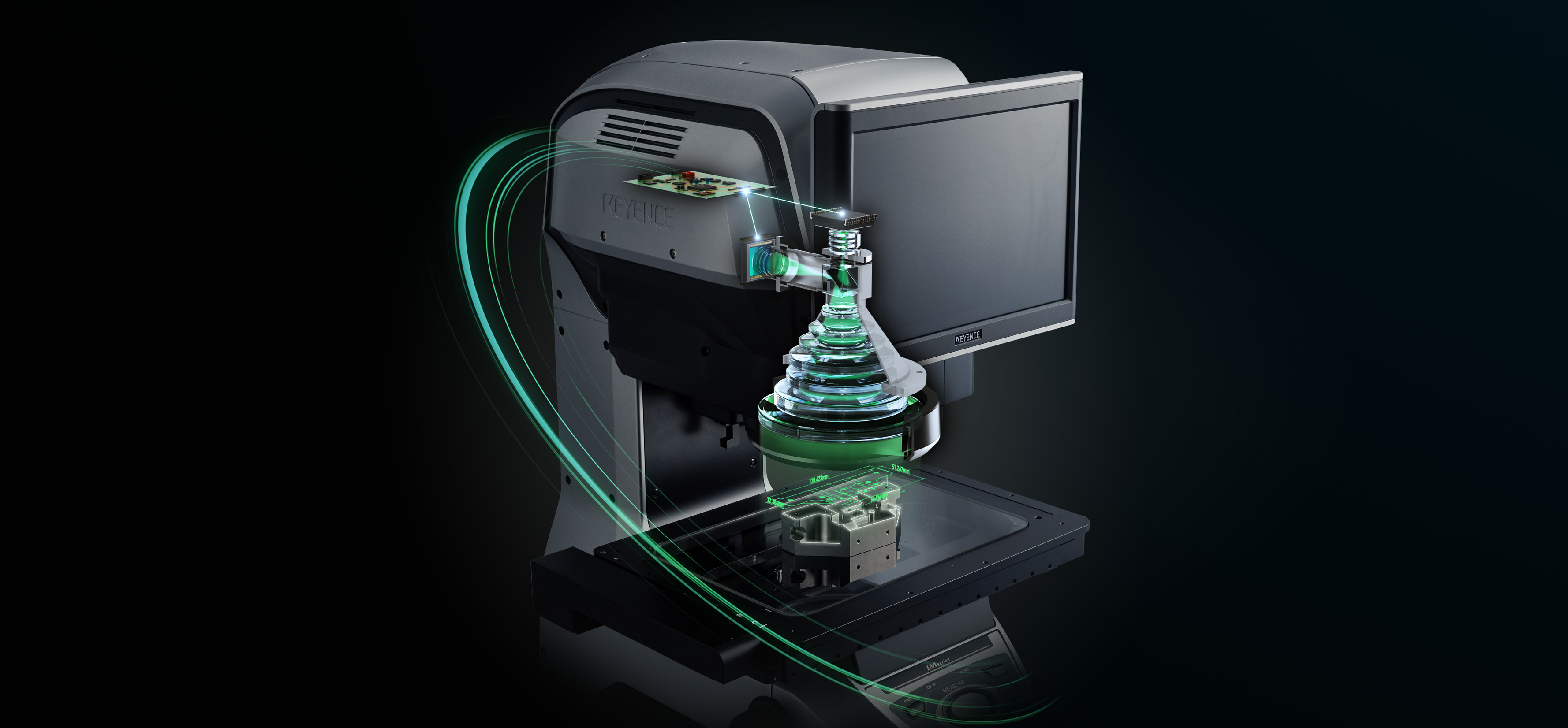
LATEST SENSOR & MEASUREMENT TECHNOLOGY IN QUALITY MANAGEMENT
Amper-Plastik invests in state-of-the-art measurement unit. After the successful introduction of a high-precision, optical 3D-coordinate-measurement unit in the year 2020, Amper-Plastik continues to invest in cutting-edge sensor and measurement technology. With the recent installation of the latest image-dimension-measurement system of the IM-8000 series from market leading company Keyence, yet another innovative measuring tool entered its service. This smart piece of technology with its exceptionally wide measurement area not only significantly increases in-house error detection capabilities and measurement speed but also features an automated CAD-drawing-data matching system.
NON-CONTACT, HIGH-PRECISION MEASUREMENT WITH AUTOMATED PRODUCT DETECTION
In the context of mass production with multiple cavities per tool, the series accompanying inspection and measuring of increasingly complex injection-molded parts is becoming a more and more costly and time-consuming challenge. Assuring a timely delivery of all products and considering the highest quality standards, the investment allows a higher degree of automation and therefore an operational added value for the standardized process.
The reduced processing time without any losses in the quality of measurement results is being achieved through various state-of-the-art features. Among those are the Keyence unit’s large measurement area of 300 x 200 mm with a maximum height of 85mm, which allows consistent measurements with automated focus adjustments on multiple parts from differing cavities within seconds. In particular, with a single push of a button it simultaneously measures up to 300 dimensions including the reliable detection of unfilled areas on up to 100 pieces, while automatically saving the data and creating inspection reports for easy processing. The quality of these measurement results is bolstered by an innovative edge detection algorithm, an ultra-high-definition 20-megapixel CMOS sensor and the intuitive software for easy adaption in the three-shift production.
DATA INTEGRATION AND CAD-DATA COMPARISON
This latest addition of sensory & measurement technology is blending in seamlessly in the overall investment strategy of Amper-Plastik, significantly increasing the digitalization and automation rate within the company. With the Keyence unit’s generated measurement data being automatically transferred to and checked against predetermined inspection parameters and CAD-drawing data. The data transfer software also ensures the documentation of the results in the CAQ-system. Once stored, the data is utilized as part of the greater data pool of the company, which combines data such as MoldFlow-simulations, 3D-scanning results, and molding machine data for an early detection of potential pitfalls. Following the holistic approach of the project management of Amper-Plastik, this integrative data gathering, and analysis benefits all departments - from order management to shop floor and up to the delivery of 100% quality-proven products.